Our Guide to Handmade Pottery in Cornwall
Creatives in Cornwall are often lured in by the natural landscape here, whether it’s the famous golden light in the sky, or the rich clay in the ground. Inspired by the ever-changing scenery and dynamic natural forms in Cornwall, not to mention an abundance of clay, this county has a long legacy of experimental ceramicists finding their feet and thriving here.
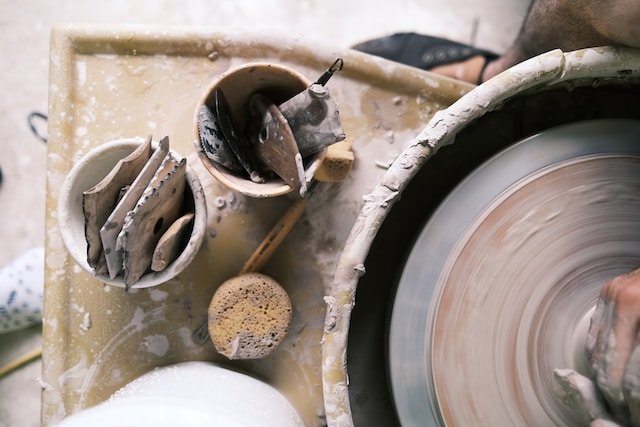
A Quick History of Cornish Pottery
There are many different branches of pottery in Cornwall, under different names. Perhaps the most renowned is the Leach Pottery, founded in St Ives by Bernard Leach and Shoji Hamada in 1920. A home for expert teaching and nurturing creative freedom, the Leach Pottery has greatly influenced pottery in the UK and the world. More commercially, the famous thick blue and white stripes of Cornishware are instantly recognisable. Legend has it, the now-famous stripes reminded an employee of the blue skies and white-crested waves of Cornwall.
Today, there are many lone Cornish ceramicists practising their discipline here, which has led to an incredibly diverse range of Cornish pottery. Our own selection of ceramicists at Inspire Makers is just a small, but perfectly curated sample of them, with each offering something unique.
What pottery is made in Cornwall?
Cornwall’s landscape is abundant in minerals. Large deposits of China clay can be found in Cornwall, which is then used to make fine white porcelain. In the 18th century Plymouth based apothecary William Cookworthy made it his mission to search for a material that resembled the kaolin (China clay) being used in China. He succeeded at Tregonning Hill, and spent years refining a process to create the purest porcelain. By the early 1800’s the St Austell deposits were the largest found in the world. Fun fact – the Eden Project sits in a former China clay mine!
What are the four main types of pottery?
Types of pottery differ depending on the types of clay and the firing techniques. The main four types of pottery are porcelain, earthenware, stoneware, and ball clay. All of them can be used to make pottery, but the look and feel of the objects will vary and is influenced by the way they are glazed and fired too.
Porcelain
So, as you now know – China clay is essential in the making of porcelain. This refined clay is fired in a kiln at approximately 1200-1450 °C, which is a very high temperature in the pottery world! Porcelain is the most non-porous type of pottery, which makes it hygienic and ideal for frequent use. China clay is used for its pure whiteness, but it is tricky to work with due to its poor plasticity. This is why many potters use a combination of clays and additives to create the desired finish and allow forms to be shaped.
If all this talk of China clay porcelain has you thinking of your grandma’s precious china, think again. Cornish potters are working with porcelain to create modern homewares and vessels that show this material in a whole new light.
Amy Cooper Ceramics
At Inspire Makers we’re marvelling at the magic of porcelain daily, as we admire the work of Amy Cooper Ceramics in the shop. Amy’s porcelain ceramics are handmade in Cornwall, and are inspired by sea creatures, the seabed, and the world under the microscope.
Nicky Stone
Ceramicist Nicky Stone starts each day with a sunrise sea swim before heading to work in her studio at the top of her garden in Falmouth. Her enchanting figures are created from high fired porcelain, and inspired by her experience of being in her world, her connection to others, the earth, sea, and stars.
Nicky’s beautiful ceramics are incredibly sought after, and she has exhibited extensively throughout Cornwall and the UK. After taking a pause, Nicky has returned to her ceramics practice and we are so honoured to stock her work.
For the ceramics lover, and sea swimmer in your life, these extraordinary sculptures are forever pieces to be cherished and passed on.
Earthenware
Earthenware is made from a rougher, more basic clay which can be found easily, often originating from riverbeds. It is known as ‘potter’s clay’ because it can easily be shaped by hand or thrown on a potter’s wheel. More porous than stoneware or porcelain, Earthenware is fantastic for holding plants! Fired at relatively low temperatures of 1000-1200°C, earthenware objects usually have the warm, rich tones of the clay they are made from. Terracotta is made from an Earthenware clay. To make Earthenware waterproof, it is often glazed, which is the process of coating the object in a glasslike substance to seal it, making it nonporous.
Stoneware
Stoneware appeared after earthenware and is more durable than both earthenware and porcelain. It is ball-clay based (more on this below), with other clays and minerals mixed in. It is a dense pottery that has a slight sandy/textural finish, due to retaining particles and oxides. Fired at the high temperatures of 1200-1300°C, stoneware is waterproof once fired and doesn’t need to be glazed to become non-porous.
Ball clay
To explain ball clay, we first look back at China clay. China clay (kaolin) is the result of decomposing minerals in Granite. A rock in plentiful supply in Cornwall! Ball clay is kaolin that has been moved by water, picking up impurities and breaking down into smaller particles on the way. Because of this it is very high in plasticity – a property which allows it to be formed and deformed, holding its structure. Often combined with other clays to control casting and improve workability, ball clay is often mixed into many potter’s clay recipes!
What are the most common types of firing clay?
Just as different combinations affect the final durability and appearance of ceramics, so does the firing process.
Electric or gas kiln
The most commercially viable way of firing clay is in an electric or gas kiln. The majority today are electric, and these chambers can reach incredibly high temperatures. Electric kilns are lined with coiled metal elements, which a current flows through generating heat, and then the processes of conduction, convection and radiation, heat, harden and dry the ceramics. Kilns are easy to use and are low maintenance, so potters can continue their making process while the kiln makes their studio nice and toasty in the background.
Wood firing
A wood fired kiln requires more maintenance but is worth the labour of love. Firings can last as long as 10 days, at temperatures of up to 1500°C. The wood burning process can be split into two stages. Firstly, the wood burns and produces gases, and you’ll spot long flames. Secondly the charcoal burns, producing incredibly hot but short flames, producing a higher heat than the original gassified wood. Often characterful details result from wood-firing, such as speckles of ash, or flame marks, making each piece unique.
Bridie Maddocks
We stock the work of the fantastic Cornwall based potter Bridie Maddocks, who creates woodfired, soda glazed stoneware. Each piece is made by hand in Penryn, and she fires in Devon three times a year.
Soda firing
Soda (sodium carbonate) can be mixed with water and introduced to the kiln at peak temperatures. The soda vaporises and reacts with the hot clay, to create mesmerising flashes of colour and glaze. This isn’t done in electric kilns as the corrosive soda will destroy the elements!
Raku
Raku firing is a dramatic process combining the elements, earth, air, fire and water. This ancient Japanese technique creates a unique finish on ceramics. While glowing red hot, glazed pieces are taken from the kiln and added to combustible material, such as sawdust, newspaper or natural elements such as leaves. By starving the ceramic of oxygen, a show stopping sheen of multiple colours is formed.
Sawdust
A sawdust kiln is one of the easiest ways to fire clay at home. Disclaimer – we recommend extensive research and testing first! Inside a simple brick chamber, pottery is submerged in sawdust, at the top of which a fire is lit and then kiln covered once burning well. A sawdust firing can take anywhere from twelve hours to three days and gives pots a rich black surface without needing a glaze.
Pit firing
Pit firing often refers to pottery that has been fired in an outdoors open bonfire pit. Black markings occur from the heavy smoke generated. Pots fired this way are often decorative and not functional, as they are porous and not glazed. The resulting ceramics are a thing of beauty, and the continuation of traditional pit firing techniques is important to the heritage of many.
Glazing Cornish Pottery
Pottery doesn’t have to be glazed, but not only does it produce an aesthetically pleasing smooth and glossy finish, it also seals the piece, making it waterproof and hygienic. Glazes are made up of three basic components: a glass-forming substance (silica or boron trioxide), a stiffening component (alumina) and a flux component. Potters tweak their glazes by adding chemicals and minerals, to achieve different finishes. Common colourants are copper carbonate, copper oxide, iron oxide and cobalt oxide, and it’s a game of trial and error as the colour changes once fired!
Michelle Foote
Ceramicist Michelle Foote is an expert when it comes to glazes, and considers which glaze will best suit her beautiful designs. Michelle works on her traditional Leach kick wheel from her garden studio in St Ives, and is inspired by the coast and nature surrounding her, often using shells to make marks in her vessels, which are highlighted by her chosen glaze.
What Is So Special About Handmade Pottery?
So why do we continue to be captivated by handmade pottery? Pottery is one of the oldest forms of art, and it has developed alongside civilisation. The oldest ceramic object found dates as far back as 28,000 BCE! The practice of taking minerals from the earth and using fire to form vessels is an artisanal technique, and one that requires not only creative skill but an understanding of the chemical reactions that occur. Potters in Cornwall today are putting their own stamp on an ancient art, inspired by the landscape that surrounds them. Handmade pottery in Cornwall is a way for creatives to express themselves, and create forms and objects that pay tribute to time honoured traditions.
A few of our other Cornish Pottery Makers!
Lucie Sivicka
Czech potter Lucie Sivicka lives in Penzance, and creates her characterful pottery just a stone’s throw away in the fishing village of Newlyn. With a rich and varied career as a ceramicist, Lucie has made pottery in Prague for other companies alongside her own practice, and held workshops in hospitals, orphanages, and schools.
Having fallen completely in love with the Cornish coast, Lucie’s ceramics today explore the hardy community of sea swimmers. Her hand painted mugs, bowls, cups, and decorations are whimsical and beautiful. They are incredibly popular as gifts for sea swimmers!
Lynne Speake
Ceramicist Lynne Speak works with porcelain paper clay to create unique forms inspired by the richness and texture found in surfaces decaying around us. Paper clay is much stronger than ordinary clay as the addition of cellulose paper fibres allows the creation of “impossible” shapes. The fibres burn out during firing and becomes lighter than traditional porcelain.
Sarah Cooling
Working from her Krowji studio in Redruth, ceramicist Sarah uses layered slips and glazes and a “sgrafitto” technique where they are scratched away to reveal the nature of her chosen materials underneath. Her ceramics are a thing of beauty, these refined forms are tactile and luxurious, and testament to Sarah’s skill.
Frances Spice
Frances is a ceramicist based here in Cornwall, working from her small summer house in her garden. Her work is slab-built and hand-modelled, which lends them a lovely tactile nature. She also skillfully adds interest by imprinting lace and wallpaper.
Frances’s subtle colour palettes add delicate interest to her pieces and tell the story of her inspiration. These contemporary handbuilt ceramics make for wonderful gifts, as they are quietly interesting and incredibly special. See her collection here.
Sarah Sullivan
How beautiful are these carved stoneware vessels by Cornwall-based ceramicist Sarah Sullivan? Sarah hand carves each piece using a small stripping tool, in a slow rhythmic process that is endlessly satisfying.
The tactile vessels are then finished in a dolomite glaze and combination of slips and glazes in a colour palette that reflects the local beach where she swims year-round. Brave!
Pots made from Cornish Clay
Potting in Penryn
Cornish potter Lisa is the face behind Potting in Penryn. Lisa’s stoneware pottery is made using Cornish clay, processed right here in the county. Her wonderful pots are simple in form, and experimental in glaze, with each one having its own identity.
Explore our shop to support a Cornish Potter
If you’re just as in awe of the skill required to make such beautiful vessels, head to our shop to see ceramics made in Cornwall. Each ceramicist offers a style or practise which is completely unique to them, and their Cornish pottery makes any home a brighter place!
Want To Hear More? We Would Love To Hear From You.
Sign up to the Inspire Makers newsletter for monthly updates on makers, workshops and exhibitions.